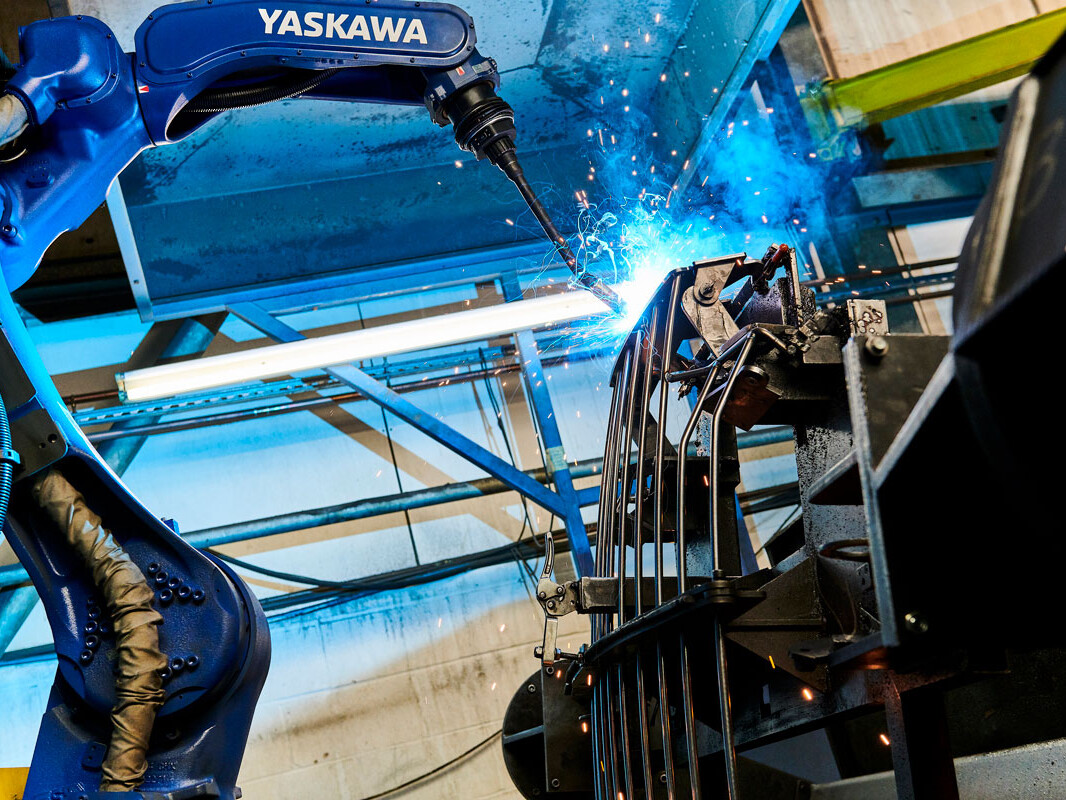
Versatile and Capable
Newfield’s welders use both Metal Inert Gas (MIG) and Tungsten Inert Gas (TIG) in a variety of medium to high volume applications, all certified to IATF 16949. We are able to provide Just in Time (JIT) supply, Kanbans and implement Enterprise Resource Planning (ERP).
From support with product design through to cost reductions via a Value Analysis and Value Engineering (VAVE) process, Newfield can work with you from the beginning to hit quality, design and budget targets.
Newfield’s MIG and TIG welding team receive continuous training to maintain their exceptional level of work. While each process has its advantages, our welders maintain a number of skill sets allowing us to easily accommodate a variety of different projects.
We also ensure our welders have the right equipment and have recently invested in new ESAB MIG welding sets. We believe that providing our professionals with the right tools is essential to the standard of work we produce.
Read our handy guide to the differences between MIG and TIG welding.
More Information
MIG Welding
MIG welding is an abbreviation for Metal Inert Gas welding, also known as Gas Metal Arc Welding (GMAW). It is a process developed in the 1940s and is considered semi-automated.
MIG welding requires three things; electricity to produce heat, an electrode to fill the joint, and shielding gas to protect the weld from the air. MIG welding is done using a very small electrode that is fed continuously, while the operator controls the amount of weld being produced.
The equipment used automatically regulates the electrical characteristics of the arc. The only manual controls required of the welder in semi-automatic operation are travel speed, travel direction and gun (torch) positioning.
Given proper equipment settings, the power supply will provide the necessary amperage to melt the electrode at the rate required to maintain the pre-selected arc length (voltage). As the welder squeezes the trigger of the MIG gun, the electricity charges the electrode while the feeder starts feeding the filler wire, creating the weld material. The shielding gas is also fed through the MIG gun nozzle, isolating the weld from the surrounding air and preventing contamination.
Filler metal selection is closely matched to the base material. The filler metal not only conducts electrical current to the arc zone, melting the base metal and electrode, it also adds reinforcement to the completed weld joint.
MIG Welding can be used with a wide variety of metals and base metal thicknesses. Its successful application depends on the appropriate selection of:
- Electrode – composition, diameter and packaging
- Shielding Gas – type (composition), purity and flow rate
- Process Variables – current, voltage, mode of metal transfer and travel speed
- Equipment – power source, welding gun and wire feeder
TIG Welding
Tungsten Inert Gas (TIG), also known as gas tungsten arc welding (GTAW), was originally created by the aircraft industry to weld magnesium in the 1930s and 1940s. It uses the heat generated by an electric arc struck between a non-consumable tungsten electrode and the workpiece. This heat fuses the metal in the joint area and produces a molten weld pool. The arc area is shrouded in an inert gas shield to protect the weld pool and the electrode from oxygen contamination.
The process may be operated autogenously, that is, without filler, or filler may be added by feeding a consumable wire or rod into the established weld pool. TIG produces very high-quality welds across a wide range of materials with thicknesses up to about 8 or 10mm. It is particularly well suited to the welding of sheet material.
One of the greatest advantages of TIG welding is the amount of control it allows. A welder can control heat and amperage with precision using a foot or thumb remote control switch. The TIG gun is thin, which adds to the control a welder can have over the process.
The success of TIG welding hinges on various factors such as the choice of shielding gas, welding wire, tungsten electrode and the user’s technique. The finished product is a sound, slag-free weld that shares the same corrosion resistance properties as the parent metal.
The differences between MIG and TIG welding
MIG and TIG welding both use an electric arc to fuse metal components together. The major difference between MIG and TIG welding is that one process uses a continuously feeding wire (MIG) and the other uses long welding rods that are slowly fed into the weld pool (TIG). TIG is by far the more difficult to learn but both are hard to master.
A MIG welder works by using a continuously feeding spool of welding wire that burns, melts and fuses both the base and parent metals together. You can weld a variety of materials such as mild steel, stainless steel and Aluminium. A range of material thicknesses can be welded from thin gauge sheet metal right up to heavier structural plates. Because it uses filler material, MIG welding often performs better for welding thicker objects, since it doesn’t have to heat the material all the way through to form a bond. Also, the use of filler material makes it slightly easier to control than TIG welding.
TIG welding, on the other hand, can join objects without filler by heating the surfaces to the point where they bond, creating neater welds. It does, however, require a great degree of precision to avoid over-heating the metal, which can cause stress cracks and other issues. TIG welding is more commonly used for thinner gauge materials and is used for things like kitchen sinks and toolboxes. The biggest benefit is that you can use relatively low power and avoid blowing through the metal. It is a much finer and delicate technique that results in a more aesthetic weld.