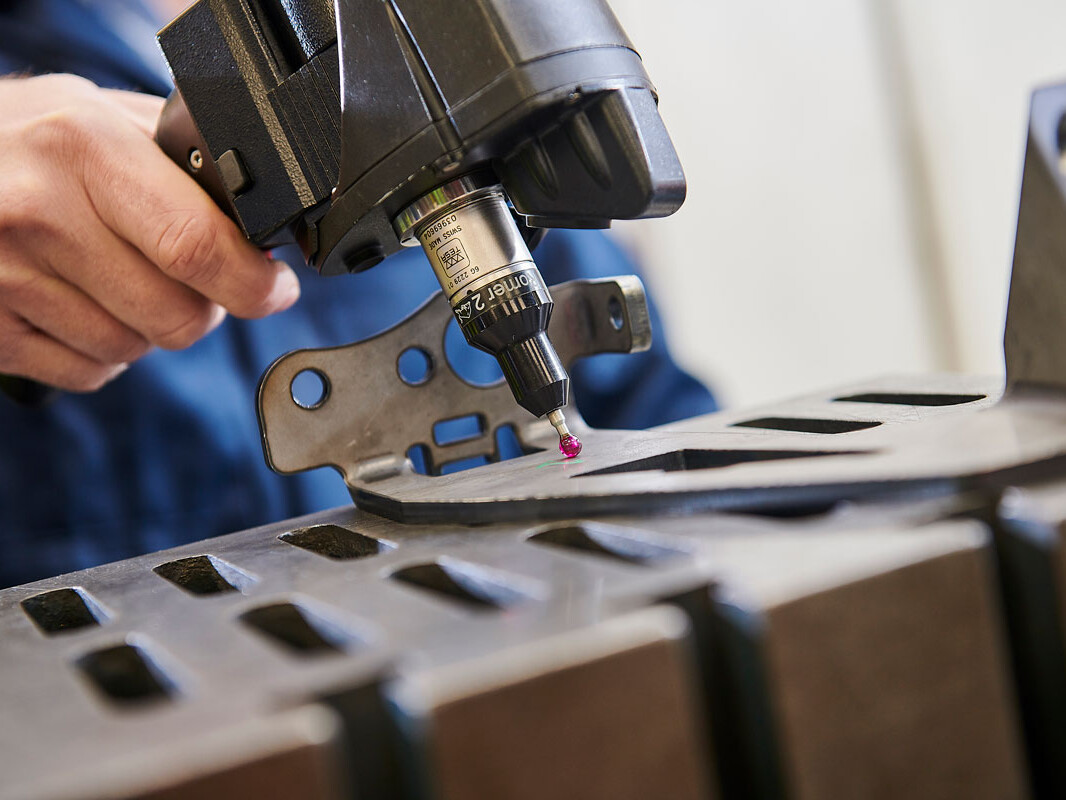
Our Accreditations
Newfield Fabrications is accredited to both IATF 16949 and ISO 9001:2015 standards. We have earned a reputation for the quality of our work and strive to maintain this with all our customers. We have an established ‘zero waste’ culture and strive to minimise risk through our data-driven continuous improvement processes.
Our Team
Our Quality Team has over 200 years’ experience in the industry. Their ability to rapidly respond to any quality issues that might arise during production is central to Newfield’s high standards. Not only do they carry out routine component inspection, but they are also able to use portable equipment to carry out spot checks at any point in the production process. Each member of the team is trained in the key quality tools associated with IATF 16949, including measurement techniques, auditing, the use of PFMEA, control plans and standard operating procedures.
Our Equipment
Our ongoing investment in the latest equipment and tools keeps Newfield at the forefront of the fabrication industry. From our advanced 10kW laser cutter to our 230-tonne automated bending machine, we believe that to provide our customers with the highest possible quality products we must equip our skilled operators with class-leading equipment. Our ongoing investment in automated processes reduces the risk of errors and helps to improve product consistency. We conduct regular measurement system analysis (MSA) studies and monitor the process capability index (CPK) of all our processes, taking action accordingly.
Our Philosophy
Here at Newfield, we understand that Safety is paramount in any work environment. We also understand that in order to work safely, processes must be as robust as possible – considering any potential risks to individuals, equipment and products. For this reason, our entire Quality Management System is designed around the Plan, Do, Check, Act methodology.
Problem-Solving
We understand that mistakes and errors are a possibility, but we know the importance of rectifying them as quickly and effectively as possible. Our Continuous Improvement philosophy emphasises problem-solving and the prevention of recurrence. However, we do not just apply it to mistakes, it is also utilised as an improvement tool to map processes and remove any non-value added (NVA) operations – reducing customer costs. Newfield operates using the 8D problem-solving method, with all Team Leaders trained to implement the technique.
More Information
The Eight Disciplines of Problem Solving (8D) is a problem-solving methodology designed to find the root cause of a problem, devise a short-term fix and implement a long-term solution to prevent recurring problems. When it’s clear that your product is defective or isn’t satisfying your customers, an 8D is an excellent first step to improving Quality and Reliability.
Ford Motor Company developed this problem-solving methodology, then known as Team Oriented Problem Solving (TOPS), in the 1980s. The 8D problem-solving process is a detailed, team-oriented approach to solving critical problems in the production process. The goals of this method are to find the root cause of a problem, develop containment actions to protect customers and take corrective action to prevent similar problems in the future.
The strength of the 8D process lies in its structure, discipline and methodology. 8D uses a composite methodology, utilising best practices from various existing approaches. It is a problem-solving method that drives systemic change, improving an entire process in order to avoid not only the problem at hand but also other issues that may stem from systemic failure.
Training
All of our production Team-Leaders have received external training on Problem Solving techniques based around the Global 8D concept. This ensures that when a problem occurs, they are able to offer invaluable insight into potential causes as well as solutions and are actively involved in problem-solving.
How do we apply it?
As stated previously, all our Team-Leaders have received training on problem-solving and Global 8D, but how do we utilise this? Here at Newfield, we accept that as humans, we can make mistakes. And when this happens, we need to act quickly to identify what the cause was and implement corrective actions to prevent a recurrence. In order to do this, we have a bespoke system in place that tracks all quality concerns reported both internally and externally.
Our 8D methodology:
Stage 1 – Define the problem
Before you can fix any problem, you must define what this problem is (who, what, where, when); this is part of the “Plan” process within the PDCA methodology.
Stage 2 – Select your team
Because of the training received, our Team-Leaders and their operators are involved very early on. Typically, our problem-solving teams consist of the Team-Leader of the process, the operators involved, a member of our Engineering team, at least one member of the Quality Team and a member of the Continuous Improvement Team. This team is typically the same team as those involved in the PFMEA and Control Plan reviews mentioned earlier.
Stage 3 – Contain
This stage must be completed within 24 hours of the problem being reported and involves checking all inventory on-site for the issue as well as any WIP (Work in Progress). This stage also involves putting a system in place temporarily to prevent any escapes to the customer whilst the root cause is determined and actioned.
Stages 4 & 5 – Root Cause
At Newfield, we focus on two elements of Root Cause Analysis; how did it happen and how did it escape? This ensures that wherever possible, we implement actions to prevent recurrence of the fault, but we also address why the fault was not detected at the time it occurred. This is done using various problem-solving techniques such as 5Why’s, Fishbone diagrams and process flows to identify any variation in the process that can be eliminated.
Stage 6 – Implementation of Corrective Action
Now that the Root Cause has been determined, the team must plan the required corrective action and then implement.
Stage 7 – Verification
This stage involves a member of the Quality team ensuring that any corrective action is effective and efficient and that the Root Causes have been addressed.
Stage 8 – Read-Across
At this stage, we look at how the problem occurred and how it was solved and see if it can be applied to similar parts and/or processes to prevent problems before they occur. This is part of our Continuous Improvement ideology here at Newfield.
All 8Ds raised are documented along with any evidence such as photos and are trended within our problem-solving system to identify any common areas which require improvement. This also involves conducting Pareto analysis on a regular basis and providing feedback to the production team.
Production Part Approval Process (PPAP) is an invaluable quality tool used in order to provide customers with a detailed understanding of the processes to be used to manufacture their product(s). In today’s competitive manufacturing environment, we understand that controlling cost and maintaining a high level of quality have become vital to success. Therefore, it has become imperative to provide quality parts that meet the customer’s requirements the first time and every time.
Elements of PPAP
Below is the list of all 18 elements accompanied by a brief description for each element:
1. Design Documentation
Design documentation shall include both a copy of the customer and our drawings as well as a copy of the Purchase Order (PO). The PO is used to confirm that the correct part is being ordered and that it is at the correct revision level. The design engineer is responsible for verifying that the two drawings match and all critical or key characteristics have been identified.
Material composition information is required to supply evidence that the material used to manufacture the parts meets the customer’s specific requirements.
2. Engineering Change Documentation
If the PPAP is being required due to a request for a change to a part or product, the documentation requesting and approving the change must be included in the PPAP package. This documentation usually consists of a copy of the Engineering Change Notice (ECN), which must be approved by the customer engineering department.
3. Customer Engineering Approval
When required as part of the PPAP, we will provide evidence of approval by the customer engineering department. If required, pre-PPAP samples are ordered by the customer for onsite testing. The samples must be production intent and ship with a waiver so that testing can be done. When testing is complete, the test engineers will provide an approval form for inclusion in the PPAP submission.
4. Design Failure Mode and Effects Analysis
Design Failure Mode and Effects Analysis (DFMEA) is a cross-functional activity that examines design risk by exploring the possible failure modes and their effects on the product or customer and their probability to occur. These failure modes can include:
- Product malfunctions;
- Reduced performance or product life;
- Safety and Regulatory issues.
5. Process Flow Diagram
The Process Flow Diagram outlines the entire process for assembling the component or final assembly in a graphical manner. The process flow includes incoming material, assembly, test, rework and shipping.
6. Process Failure Mode and Effects Analysis
Process Failure Mode and Effects Analysis (PFMEA) reviews all of the steps in the production process to identify any potential process quality risk and then document the applied controls. The PFMEA is also a living document and should be updated even after the product is in normal production.
7. Control Plan
The Control Plan is an output from the PFMEA. The Control Plan lists all product Special Characteristics and inspection methods required to deliver products that continually meet the customer quality requirements.
8. Measurement System Analysis Studies
Measurement System Analysis (MSA) studies will include Gage Repeatability & Reproducibility (GR&R) studies on measurement equipment used during assembly or quality control checks. Calibration records for all gages and measurement equipment must be included.
9. Dimensional Results
The dimensional layout of sample parts is required to validate the product meets the print specifications. The samples should be randomly selected from a significant production run usually at least 30 pieces. Each dimension on the drawing is measured on the final assembly to make sure that it falls within specification. The results are recorded in a spreadsheet and included within the PPAP submission.
10. Records of Material / Performance Tests
This element should contain a copy of the Design Verification Plan and Report (DVP&R). The DVP&R is a summary of every validation test performed on the part. It should list each and every test performed, a description of how the test was performed, and the results of each test.
This section typically includes copies of all the certification documents for all materials listed on the prints. The material certification shall show compliance to the specific call on the print.
11. Initial Process Studies
Initial process studies will be done on all the production processes and will include Statistical Process Control (SPC) charts on the critical characteristics of the product. These studies demonstrate that the critical processes are stable, demonstrate normal variation and are running near the intended nominal value.
12. Qualified Laboratory Documentation
Qualified laboratory documentation consists of the industry certifications for any lab that was involved in completing validation testing. This could be for an in-house test lab or any offsite contracted test facilities that were used for validation or material certification testing.
13. Appearance Approval Report
The Appearance Approval Inspection (AAI) is applicable for components affecting appearance only. This report verifies that the customer has inspected the final product and it meets all the required appearance specifications for the design. The appearance requirements could include information regarding colour, textures, etc.
14. Sample Production Parts
Sample production parts are sent to the customer for approval and are typically stored at either the customer or supplier’s site after the product development is complete. A picture of the production parts is usually included in the PPAP documentation along with documentation regarding the location that the parts are being stored.
15. Master Sample
A master sample is a final sample of the product that is inspected and signed off by the customer. The master sample part is used to train operators and serves as a benchmark for comparison to standard production parts if any part quality questions arise.
16. Checking Aids
This is a detailed list of checking aids used by production. It should include all tools used to inspect, test or measure parts during the assembly process. The list should describe the tool and have the calibration schedule for the tool. Checking aids may include check fixtures, contour, variable and attribute gages, models or templates.
MSA may be required for all checking aids based on customer requirements.
17. Customer Specific Requirements
This element of the submission package is where any special customer requirements are contained. For bulk materials, the customer-specific requirements shall be recorded on the “Bulk Material Requirements Checklist”.
18. Part Submission Warrant
The Part Submission Warrant (PSW) form is a summary of the entire PPAP submission. A PSW is required for each of part number unless otherwise stated by the customer. The PSW includes:
- The reason for submission (design change, annual re-validation, etc.);
- Supplier authorized person signature along with contact information;
- A section provided for any required explanation or comments;
- An area for the customer to indicate the disposition of the PPAP;
- Declaration of part conformity to customer requirements;
- The level of documents submitted to the customer.
The PPAP process is a detailed and lengthy process. The PPAP package includes documentation of various multiple cross-functional tools and documents our ability to meet all customer requirements. The PPAP provides customers adequate information to validate that all areas of the design and production processes have been reviewed thoroughly to ensure that only high-quality products will be allowed to ship to the end customer
The Plan, Do, Check, Act (PDCA) methodology is one of the original quality tools and is the foundation for ISO 9001:2015. Put simply, it means that any time a process is being reviewed or developed, you must consider all factors that could cause risk and act accordingly to mitigate the risk as far as reasonably practicable. This applies to Quality as well as Safety and that is why here at Newfield, we consider ourselves to be ever-learning and ever-developing because we understand that everything can always be improved, and we continually seek to do so.
Official PDCA
The PDCA Cycle can help differentiate a company from its competition, especially in today’s corporate world, where anything that can help them streamline their processes to reduce costs, increase profits and improve customer satisfaction can give them an advantage. Whether they know it or not, many managers use the PDCA Cycle to help direct their organizations, as it encompasses the very basic tenants of strategic planning. The four components can be summarised like the following:
Plan: A well-defined project plan provides the framework from which to operate. Importantly, it should reflect the organisation’s mission and values. It should also map the project’s goals and clearly indicate the best way to meet them.
Do: This the step where the plan is set in motion. The plan was made for a reason, so it is important for players to execute it as outlined. This stage can be broken down into three sub-segments, including training of all personnel involved in the project, the actual process of doing the work and recording insights, or data, for future evaluation.
Check: Typically, there should be two checks throughout the project. First, checks should be done alongside the implementation to make sure that the project’s objectives are being met. Second, a more comprehensive review of the project should be done upon completion to allow for successes and failures to be addressed, and for future adjustments to be made.
Act: Corrective actions are made in the final step. Once past mistakes have been identified and accounted for, the PDCA Cycle can be redefined and repeated anew in the future, perhaps to better results under new guidelines.
PDCA and Continuous Improvement
Companies looking to enhance their internal and external processes often deploy PDCA methodology to minimize errors and maximize outcomes. Once put into effect, companies can repeat the PDCA cycle and make it a constant in their organization as something of a standard operating procedure. That one of the four stages is to deploy corrective actions makes the methodology ideal to strive for continuous improvement.
Statistical Process Control
Statistical Process Control (SPC) is an industry-standard methodology for measuring and controlling quality during the manufacturing process. Quality data in the form of Product or Process measurements are obtained in real-time during manufacturing. This data is then plotted on a graph with pre-determined control limits. Control limits are determined by the capability of the process, whereas specification limits are determined by the customer specifications.
Data that falls within the control limits indicate that everything is operating as expected. Any variation within the control limits is likely due to a common cause—the natural variation that is expected as part of the process. If data falls outside of the control limits, this indicates that an assignable cause is likely the source of the product variation, and something within the process should be changed to fix the issue before defects occur.
Statistical Process Control enables you to:
- Dramatically reduce variability and scrap
- Scientifically improve productivity
- Reduce costs
- Uncover hidden process personalities
- Instantly react to process changes
- Make evidence-based decisions on the shop floor
Measurement System Analysis (MSA)
MSA is defined as an experimental and mathematical method of determining the amount of variation that exists within a measurement process. Variation in the measurement process can directly contribute to our overall process variability. MSA is used to certify the measurement system for use by evaluating the system’s accuracy, precision and stability.
MSA is a collection of experiments and analysis performed to evaluate a measurement system’s capability, performance and amount of uncertainty regarding the values measured. We should review the collected measurement data as well as the methods and tools used to collect and record it. Our goal is to quantify the effectiveness of the measurement system, analyse the variation in the data and determine its likely source.
Put simply, we continuously verify that all of our processes are as effective and efficient as possible, and this also includes our inspection/checking processes. We review the variation to determine how accurate our measurement systems are which ensures we are always performing to customer expectations.
Advanced Product Quality Planning (APQP)
Complex products and supply chains present plenty of possibilities for failure, especially when new products are being launched. Advanced Product Quality Planning (APQP) is a structured process aimed at ensuring customer satisfaction with new products or processes. APQP has existed for decades in many forms and practices and is used by progressive companies to assure quality and performance through diligent planning to ensure any new process has had all potential issues considered and addressed prior to going “live”.
APQP is a structured approach to product and process design. This framework is a standardized set of quality requirements that enable suppliers to design a product that satisfies the customer. The primary goal of product quality planning is to facilitate communication and collaboration between engineering activities. A Cross Functional Team (CFT), involving marketing, product design, procurement, manufacturing and distribution, is used in the APQP process. APQP ensures the Voice of the Customer (VOC) is clearly understood, translated into requirements, technical specifications and special characteristics. The product or process benefits are designed in through prevention.
Failure Mode and Effect Analysis (FMEA)
Failure Mode and Effects Analysis (FMEA) is a structured approach to discovering potential failures that may exist within the design of a product or process. Failure modes are the ways in which a process can fail. Effects are the ways that these failures can lead to waste, defects or harmful outcomes for the customer. Failure Mode and Effects Analysis is designed to identify, prioritize and limit these failure modes. FMEA is not a substitute for good engineering. Rather, it enhances good engineering by applying the knowledge and experience of a Cross Functional Team (CFT) to review the design progress of a product or process by assessing its risk of failure.
Control Plans
A Control Plan is a method for documenting the functional elements of quality control that are to be implemented, ensuring quality standards are met for a particular product or service. The intent of the control plan is to formalize and document the system of control that will be utilised.
Put simply, a control plan is a live document that details all potential failures within a process as well as the controls that we have put in place to reduce their likelihood as far as reasonably practicable.
Layered
In order to ensure that our processes are performing as expected, we operate a layered-audit system which means that regular audits are conducted by 3 distinct levels of our team; Team-Leaders, Senior Management and Directors. This ensures that we are not only constantly monitoring processes but also that we are doing it in a varied way, providing us with as much information as possible. All individuals who conduct audits are trained (either internally or externally) to do so and all audit findings are reported weekly along with corrective action taken. At Newfield, we believe in a Just culture which in turn promotes individuals to raise any concerns that they have without fear of repercussion, as stated previously we believe everything can always be improved and the best way to do this is to have an open line of communication throughout the workforce.
System (QMS)
In line with IATF 16949:2016 and ISO9001:2015 requirements, we conduct regular system audits against the requirements of our Quality Management System. These audits are conducted by employees who have been externally trained against the standards and this ensures we are constantly monitoring how we perform as a business.
Manufacturing Review
Manufacturing reviews are a crucial element of how we operate at Newfield as these enable the senior management to meet regularly and review our objectives in line with the companies Quality Policy. This is also where we review all KPIs (Key Performance Indicators) of the business including Quality, Production and Engineering to ensure that we are continuing to meet our targets.